- Case Study -
From Perfusion to Fed-Batch:
Choosing the right tech to optimize processes and reduce costs for therapeutic proteins
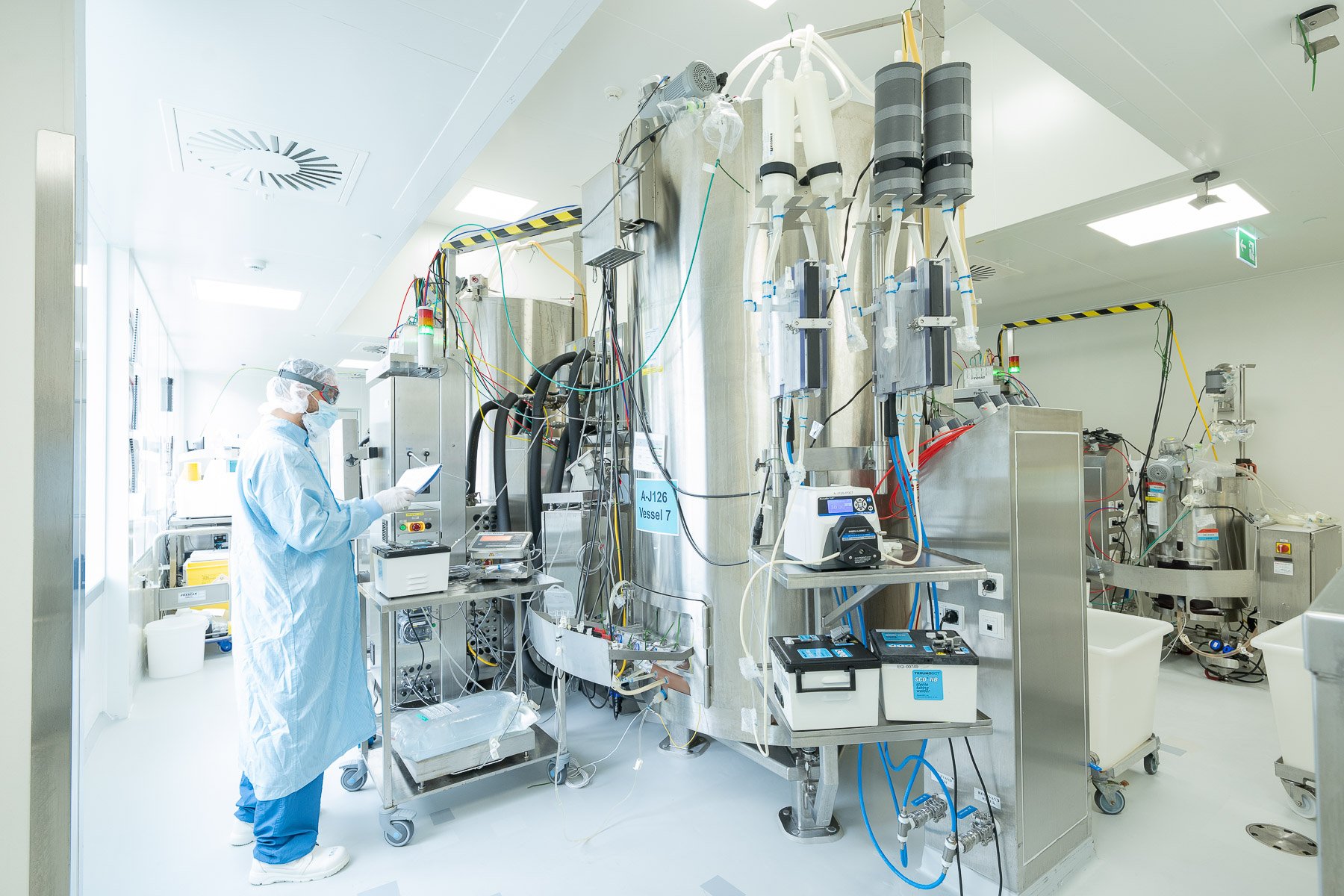
The Challenge
A biopharmaceutical company sought to develop a modified recombinant human blood clotting Factor Xa that enables normal blood clotting, even in the presence of Factor Xa blood clotting inhibitors. While their initial small-scale manufacturing process utilizing perfusion technology proved effective, the company faced significant challenges in scaling up production to meet commercial demands. Perfusion, while offering certain advantages such as fewer total steps and the use of smaller bioreactors, presented limitations in terms of scalability and cost-effectiveness due to the continuous replenishment of media and the extended process duration. These factors posed a substantial risk to the drug's market entry, as high production costs could hinder its accessibility to patients.
The company recognized the need for a more efficient and scalable manufacturing strategy to ensure the successful commercialization of their therapeutic protein. They sought a solution that would not only enhance productivity but also significantly reduce costs, making the drug more accessible to patients in need.
The AGC Biologics Solution
AGC Biologics partnered with the company to address these manufacturing challenges and ease path to market. Through a meticulous and data-driven approach, AGC Biologics conducted a comprehensive analysis of the existing perfusion process, including metabolomics studies to identify key metabolic pathways influencing protein activity.
Leveraging these insights, AGC Biologics' team of experts devised a strategic shift from perfusion to fed-batch and intensified fed-batch processes. This innovative approach involved optimizing nutrient delivery, cell growth conditions, and process parameters to maximize productivity while maintaining stringent product quality standards. By strategically feeding nutrients to the cell culture only when depleted, the fed-batch process reduced media consumption and shortened the overall process duration compared to perfusion. The intensified fed-batch process further enhanced productivity by fine-tuning nutrient delivery and cell growth conditions, resulting in higher product yields.
The Results
Substantial Cost Reduction & Shortened Production Timeline
The implementation of fed-batch and intensified fed-batch processes yielded remarkable results, achieving a 65% and 53% reduction in cost of goods compared to perfusion, respectively. These significant cost reductions were primarily attributed to the lower media consumption and shorter process duration associated with fed-batch strategies. Additionally, the intensified fed-batch process proved adaptable for reducing seed train costs, further enhancing the economic viability of the manufacturing process.
By overcoming the productivity limitations of the initial perfusion process and implementing innovative fed-batch strategies, AGC Biologics enabled the company to achieve a commercially viable and scalable manufacturing solution for their therapeutic protein. This success not only accelerated the drug's path to market but also ensured its affordability and accessibility to patients. The case study exemplifies AGC Biologics' commitment to partnering with clients to develop tailored solutions that address complex manufacturing challenges and ultimately enable successful commercialization and improve patient outcomes.